2020년 배터리 데이에서 일론 머스크는 기존 습식공정으로 제작되는 전극과 다르게, 용매를 사용하지 않는 친환경적인 제조방법인 건식전극 (Dry electrode)을 소개하였다. 또한 기업 입장에서 원가를 절감할 수 있어 차세대 기술로 주목받고 있다.
그렇다면 기존의 유기용매를 사용하는 습식공정은 어떻게 진행되는지 알아보자.
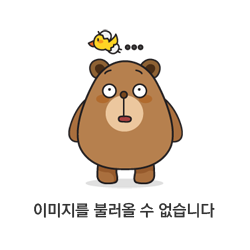
기존 습식공정은 활물질, 도전재, 바인더를 이용해 슬러리를 제조할 때, NMP라는 유기 용매를 사용한다. NMP는 전극 제조에 사용되는 재료들(활물질, 도전재, 바인더)이 잘 분산되고 섞이게 해주는 역할을 한다. 이렇게 섞인 슬러리는 극판에 Coating 공정을 지난 후 Drying 공정을 지나게 된다.
Drying 공정을 거치는 이유는 분산 용매로 사용된 NMP를 제거하기 위해서이다. 습식공정의 단점은 Drying 공정 때문이다.
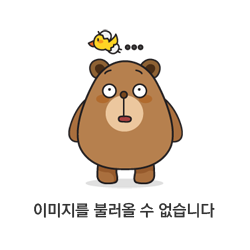
그 이유는 NMP의 물성 때문이다. NMP는 끓는점 (Boiling point)가 202도로 매우 높은 온도에서 가열해주어야 NMP가 기화되어 제거가 가능하다. 높은 열에너지를 가해야하기 때문에 비용이 많이 필요하다. 또한 연속식으로 전극 생산을 해야 하므로, Drying 공정 적용 시 필요 면적이 매우 길게 필요한 단점이 있다.
이러한 이유 때문에 가격경쟁력을 갖추기 위해서, 대량생산을 해야 하는 기업 입장에서는 건식전극이 필요하다. 건식전극의 제조공정은 매우 단순하다.
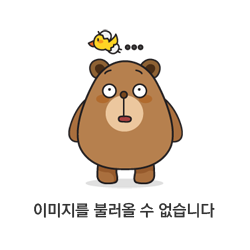
활물질, 바인더, 도전재를 용매 없이 mixing 하여 슬러리 상태로 제조해서 바로 Coating 하는 방법으로 제조한다. 다시 말해서, 기존 습식공정 대비 Drying 공정이 없어지는 것이다. Coating 방법으로 현재 널리 알려진 방법은 Free standing으로 슬러리를 전극 형태로 미리 제조해 놓고 알루미늄 극판에 Lamination 시키는 방법이 있다.
또한, 재료 측면에서 바인더가 변경되었다는 것이다. 기존 습식 방법은 (양극 : PVDF, 음극 : SBR/CMC) 바인더를 사용하였지만, 건식전극에서는 PTFE 바인더를 사용하고 있다.
이렇게 건식전극이 적용된 배터리가 생산된다면, 원가절감 측면에서 아주 효율적이라고 볼 수 있다.
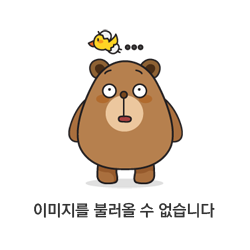
그림에 나와있듯이, 배터리 셀에서 가장 큰 비중을 차지하는 것이 전극 공정이다. 양극과 음극을 포함하면 총 35%를 차지하고 있다. 더 나아가 여러 셀이 합쳐진 배터리 팩의 경우, 셀의 제조 원가가 76%로 압도적인 것을 알 수 있다. NMP 용매를 사용하지 않아 비용이 절감될 것이고, Drying 공정에서 많은 열에너지를 절약할 수 있어 많은 경제적 이점을 누릴 것이라 예상된다.
하지만, 건식전극은 아직까지 양산될 수 없는 여러 이유들도 존재한다. 유기용매를 사용하여 분산시키지 않기 때문에 전극을 구성하는 재료들이 잘 분산되지 않는 문제점이 있다. 이에 따라 활물질, 바인더, 도전재가 균일하게 분산되지 않기 떄문에 Pressing 공정 적용 시 입자가 떨어져 나가는 문제점도 존재한다.
해당 건식전극 제조 방법은 미국의 Maxwell 이 선도하고 있으며, 실제로 테슬라는 Maxwell을 인수하였다가 다시 되팔기도 하였다. 국내에서는 한국에너지기술연구원(KIER), LG ES 등 여러 기업에서도 연구를 활발하게 진행중이다. 건식전극 공정이 적용된 배터리가 양산되지는 않았지만, 재료적인 측면이나 공정기술적인 측면이 개선되어 건식전극이 적용된 배터리가 양산되는 시대가 오길 바란다.
'이차전지' 카테고리의 다른 글
리튬이온배터리 분리막(Separator)의 역할과 특성 (0) | 2022.11.16 |
---|---|
리튬이온배터리의 음극재 : 흑연(Graphite)의 역할 및 특징 (1) | 2022.11.15 |
리튬이온배터리 NCM 양극재(Cathode)에 대한 이해와 양극재 종류 (0) | 2022.10.26 |
리튬이온배터리의 전해액(Electrolyte)의 이해와 그 종류 (5) | 2022.10.25 |
화성공정의 핵심 : SEI (Solid Electrolyte Interphase) 란 무엇인가? (0) | 2022.10.24 |
댓글